وبلاگ
انواع پرینتر های سه بعدی و روش های پرینت سه بعدی
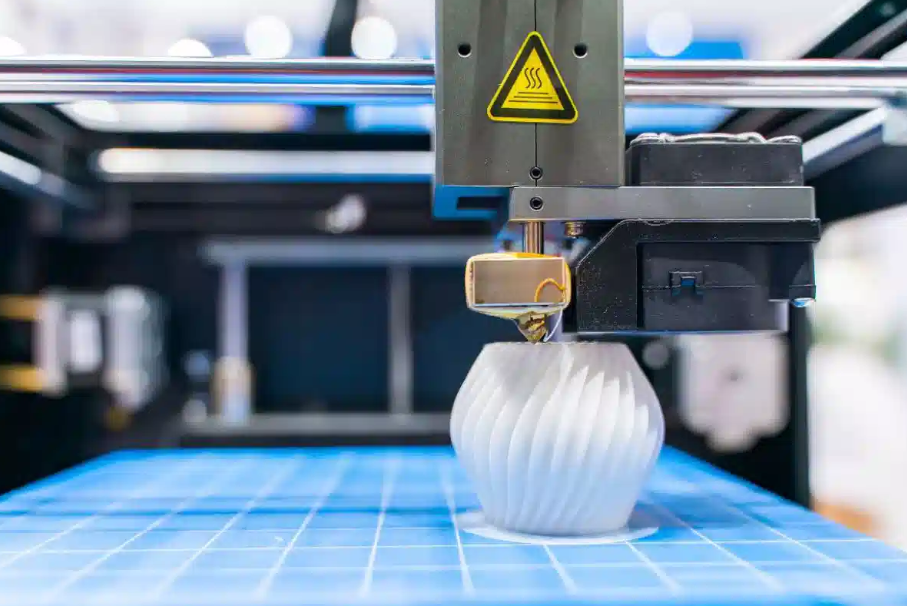
پیشرفتها به سوی یک پرینتر سه بعدی ایدهآل
فناوری پرینت سه بعدی، که به عنوان تولید افزایشی (AM) نیز شناخته میشود، به سرعت در حال توسعه است و پتانسیل ایجاد تحول در صنایع مختلف را دارد. هدف نهایی، دستیابی به یک پرینتر سه بعدی ایدهآل است که بتواند قطعات پیچیده را با سرعت، دقت و کیفیت بالا تولید کند. در اینجا به برخی از پیشرفتهای کلیدی در این راستا اشاره میکنیم:
توسعه مواد پیشرفته
توسعه مواد مصرفی پیشرفتهتر و گستردهتر برای پرینترهای سه بعدی.
بهبود سرعت و دقت چاپ
بهبود سرعت و دقت چاپ.
دقت بالا، صافی سطح مناسب.
توسعه نرمافزار
افزایش قدرت و کارایی نرمافزارهای طراحی سه بعدی.
یکپارچهسازی با فناوریهای دیگر
افزایش تعامل پرینترهای سه بعدی با سایر فناوریها مانند هوش مصنوعی (AI)، اینترنت اشیا (IoT) و واقعیت افزوده (AR).
ادغام با فناوری اسکن سه بعدی برای مهندسی معکوس.
گسترش روشهای پرینت سه بعدی
توسعه روشهای جدید پرینت سه بعدی. در حال حاضر حدود 25 تکنیک برای پرینت سه بعدی وجود دارد که حدود 10 مورد از آنها به صورت رایج در صنعت استفاده میشوند. برخی از روشهای پرینت سه بعدی عبارتند از:
FDM (مدلسازی رسوب ذوبشده)
SLA (استریولیتوگرافی)
SLS (تفجوشی لیزری انتخابی)
DLP (پردازش دیجیتالی نور)
LOM (تولید اشیا لایه لایه)
کاهش هزینهها و افزایش دسترسی
توسعه پرینترهای سه بعدی در دو حوزه: سطح خانگی و سرگرمی و سطح تولید با ارزش.
کاهش هزینههای تولید و امکان ساخت محصولات سفارشی بدون تحمیل هزینههای مازاد.
مزایای پرینت سه بعدی
امکان تولید قطعات کاربردی و عملیاتی.
استحکام و ضربهپذیری بالای قطعات.
پایداری حرارتی و شیمیایی بالا.
زیستسازگاری و کاربرد در تولید تجهیزات پزشکی.
قابلیت ماشینکاری، پولیش و رنگ.
کاهش نیاز به کار مونتاژ.
کاهش ردپای کربن تولیدی.
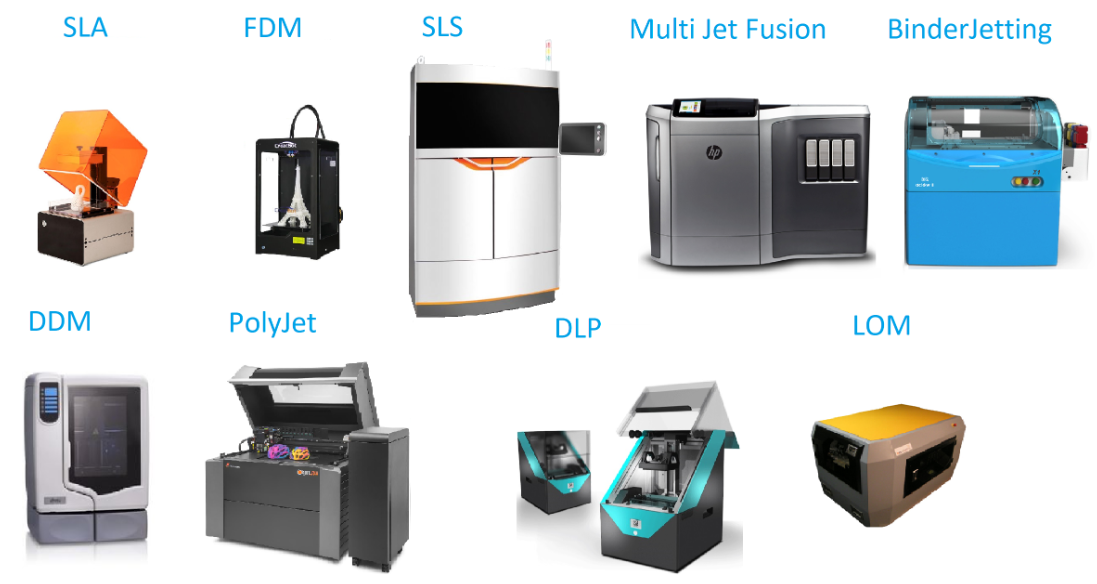
گسترش روشهای پرینت سه بعدی به شرح زیر است:
روشهای رایج پرینت سه بعدی امروزه حدود 25 تکنیک برای پرینت سه بعدی وجود دارد که حدود 10 مورد از آنها به صورت رایج در صنعت استفاده میشوند. برخی از این روشها عبارتند از:
مدلسازی رسوب ذوب شده (Fused Deposition Modeling یا FDM)
یکی از پرکاربردترین و محبوبترین روشهای چاپ سهبعدی است. این فناوری به دلیل سادگی و کارایی بالا، به ویژه در میان کاربران خانگی و صنایع کوچک، مورد توجه قرار گرفته است.
تعریف و اصول کار FDM
در روش FDM، مواد اولیه به شکل فیلامنتهای ترموپلاستیک استفاده میشوند. این فیلامنتها از طریق یک نازل گرم شده ذوب میشوند و به صورت لایه به لایه بر روی صفحه ساخت قرار میگیرند. هر لایه در حین سرد شدن به لایه زیرین خود میچسبد و بدین ترتیب یک شیء سهبعدی تشکیل میشود.
فرآیند چاپ
اکستروژن: فیلامنتهای ترموپلاستیک از طریق نازل اکسترود میشوند.
ذوب شدن: مواد در دمای بالا ذوب شده و به صورت مایع درمیآیند.
رسوب لایهای: نازل با حرکت در محورهای X و Y، مواد ذوبشده را بر روی صفحه ساخت رسوب میدهد.
سرد شدن و سخت شدن: پس از رسوب هر لایه، مواد شروع به سرد شدن کرده و به تدریج سخت میشوند.
مزایا و معایب FDM
مزایا
سادگی: FDM یکی از سادهترین روشها برای چاپ سهبعدی است که نیاز به تخصص فنی کمتری دارد.
هزینه پایین: پرینترهای FDM معمولاً نسبت به سایر فناوریها مانند SLS یا SLA ارزانتر هستند.
تنوع مواد: امکان استفاده از انواع مختلف فیلامنتهای ترموپلاستیک، شامل ABS، PLA، PETG و غیره.
معایب
کیفیت سطح: ممکن است قطعات تولید شده دارای ناهمواریهایی در سطح باشند که نیاز به پردازش بیشتر دارند.
محدودیتهای هندسی: برخی از طراحیها ممکن است نیاز به ساختارهای پشتیبانی داشته باشند که ممکن است در چاپ دشواری ایجاد کند.
کاربردها
مدلسازی رسوب ذوب شده برای تولید نمونههای اولیه، مدلهای مفهومی، و حتی قطعات کاربردی در صنایع مختلف استفاده میشود. این روش به ویژه برای کاربران خانگی و طراحان صنعتی که نیاز به تولید سریع و مقرون به صرفه دارند، بسیار مناسب است.
استریولیتوگرافی (Stereolithography) یا SLA
که با نامهای ساخت نوری، سنگچاپ سهبعدی، انجماد عکس یا چاپ رزین نیز شناخته میشود، یک فناوری چاپ سهبعدی است که در صنعت نمونهسازی سریع انقلابی به پا کرد. این روش از قدیمیترین متدها در تاریخ پرینت سه بعدی است و همچنان مورد استفاده قرار میگیرد.
نحوه کارکرد:
در این فرآیند، یک لیزر UV برای جامد کردن رزین فوتوپلیمر مایع به صورت لایه به لایه استفاده میشود تا مدلهای سهبعدی پیچیده ایجاد شوند. در هر پرینتر SLA مخزنی از رزین مایع وجود دارد و یک لیزر فوقالعاده قدرتمند این رزین را به شکل مورد نظر سخت میکند. نقاطی از رزین مایع که هدف لیزر قرار میگیرند، به حالت جامد درمیآیند و برای این هدفگیری از یک آینه استفاده میشود که توسط یک کامپیوتر کنترل میشود و لیزر را در جهت مختصات درست هدایت میکند.
مراحل پرینت سه بعدی SLA:
طراحی مدل سه بعدی: همچون بسیاری از فرآیندهای ساخت افزایشی، اولین قدم طراحی یک مدل سه بعدی در نرمافزار CAD است. فایل CAD نهایی، یک نمایش دیجیتالی از شیء مورد نظر خواهد بود.
پرینت سه بعدی به روش SLA: لیزر پرینتر SLA، طرحی از لایه اول را درون رزین حساس به نور ترسیم میکند.
انجام عملیات پسپردازش: پس از چاپ، قطعه نیاز به شستشو و پخت نهایی دارد تا به استحکام و دقت نهایی برسد.
مزایای چاپ سه بعدی استریولیتوگرافی:
وضوح بالا.
پرداخت سطح صاف.
جزئیات پیچیده.
تنوع بالای مواد.
حداقل پس از پردازش.
مناسب برای نمونهسازی سریع و توسعه محصول.
تولید قطعات با خواص مکانیکی متنوع و کاربردهای خاص.
کاربردها:
تولید مدلها.
نمونهسازی.
الگوها.
قطعات کاربردی.
جواهرات.
لوازم دندانپزشکی.
مدلهای پزشکی.
محصولات سفارشی.
این فناوری اولین بار در اوایل سال 1970 توسط هیدو کوداما، محقق ژاپنی، ابداع شد4. چاک هال در سال 1984 این اصطلاح را ابداع کرد، زمانی که او برای ثبت اختراع در مورد این فرآیند درخواست داد و در سال 1986 این اختراع به او اعطا شد.
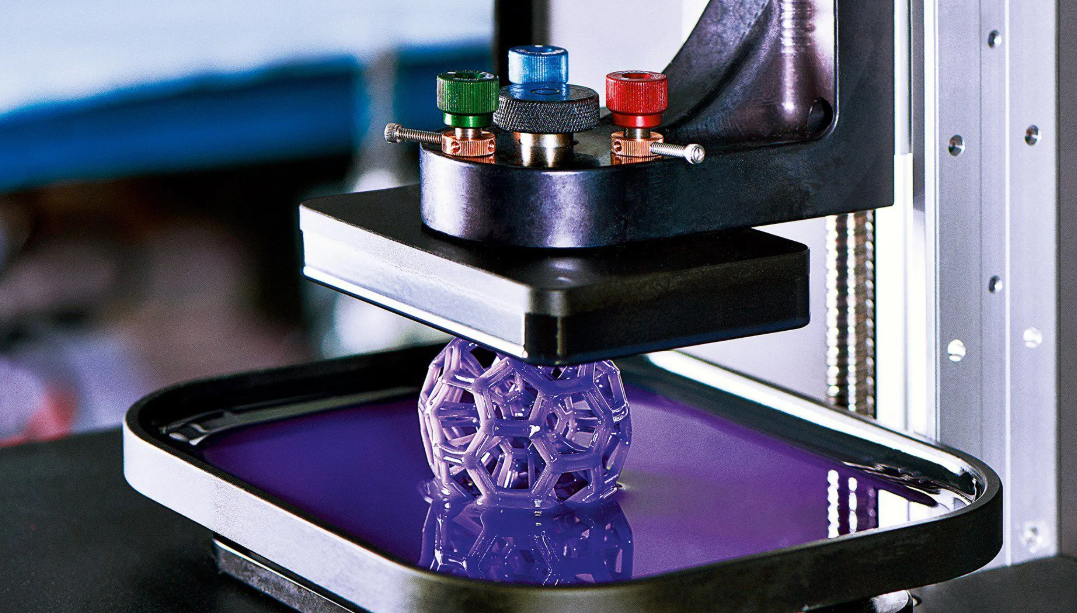
پردازش دیجیتال نور (DLP)
یکی از فناوریهای پیشرفته در دنیای پرینت سه بعدی است که از یک پروژکتور نور برای تولید قطعات دقیق و با کیفیت سطح بالا استفاده میکند. DLP نوعی از فناوری پلیمریزاسیون Vat است که در آن از رزین فوتوپلیمر مایع استفاده میشود که تحت منبع نوری فرآیند جامدسازی را انجام میدهد. در این روش، یک پروژکتور نور دیجیتال (DLP) به جای لیزر، از یک منبع نور قوی و آینههای میکروسکوپی برای تابش نور UV به سطح رزین استفاده میکند.
نحوه عملکرد پرینتر DLP:
مخزنی حاوی رزین مایع حساس به نور UV وجود دارد.
پروژکتور نور دیجیتال، تصویر هر لایه از قطعه را به صورت یکباره روی سطح رزین میتاباند و باعث جامد شدن آن لایه میشود.
این لایهها به تدریج روی هم قرار میگیرند تا جسم سه بعدی کامل شود.
پس از اتمام چاپ، قطعه از مخزن خارج شده و مراحل پس پردازش مانند شستشو و پخت نهایی را طی میکند.
پروژکتور با وضوح بالا، نور ماوراء بنفش را در همان شکلی که سطح مقطع لایه قطعه است بر روی سکوی ساخت میتاباند. طرح مقطعی با آرایهای از آینههای میکروسکوپی به نام DMD ایجاد میشود که نور را فقط در جایی که مورد نیاز است هدایت میکند. چگالی آرایه، رزولوشن چاپ را تعیین میکند.
تفاوت بین DMD و LCD در چاپ سه بعدی DLP:
در چاپ سه بعدی DLP، دو فناوری اصلی برای کنترل نور و پلیمریزاسیون رزین استفاده میشود: DMD (Digital Micromirror Device) و LCD (Liquid Crystal Display). هر دو فناوری از نور UV برای سخت کردن رزین استفاده میکنند، اما روش کنترل نور در آنها متفاوت است.
DMD (دستگاه میکروآینه دیجیتال):
شامل آرایهای از آینههای بسیار کوچک است که هر کدام به صورت جداگانه قابل کنترل هستند. با اعمال ولتاژ روی هر آینه، آن آینه میتواند بین دو حالت روشن و خاموش تغییر وضعیت دهد. زمانی که آینهای روشن است، نور UV را به سمت رزین منعکس میکند و در آن نقطه پلیمریزاسیون رخ میدهد. با کنترل دقیق موقعیت آینهها، میتوان الگوهای پیچیدهای از نور UV را ایجاد کرد که برای ساخت لایههای سه بعدی مورد نیاز است.
مزایا: رزولوشن بالا، سرعت بالا و کنترل دقیق.
معایب: هزینه بالا و پیچیدگی ساخت.
چاپگرهای نوع LCD از یک صفحه نمایش LCD به عنوان فیلتر نور استفاده میکنند و معمولاً دقت کمتری دارند.
مزایای DLP:
در مقایسه با SLA در چاپ برخی قطعهها سریعتر است، چرا که به جای ایجاد برش عرضی در هر لایه، به طور همزمان تمام لایهها را در معرض دید قرار میدهد.
تکنولوژی DLP از دقیقترین تکنولوژیهای پرینت سه بعدی محسوب میشود که میتواند جزئیات و الگوهای ظریف و ریز و قطعات کوچک با ضخامتهای پایین را با دقتی بسیار بالا تولید کند.
کاربردها:
کاربرد اصلی این پرینترها برای ساخت موم قالبهای مستقیم ریخته گری دقیق و قالبهای غیرمستقیم در صنعت طلا، جواهر و زیورآلات است. در برخی صنایع پزشکی و به خصوص دندانپزشکی نیز کاربرد دارند.
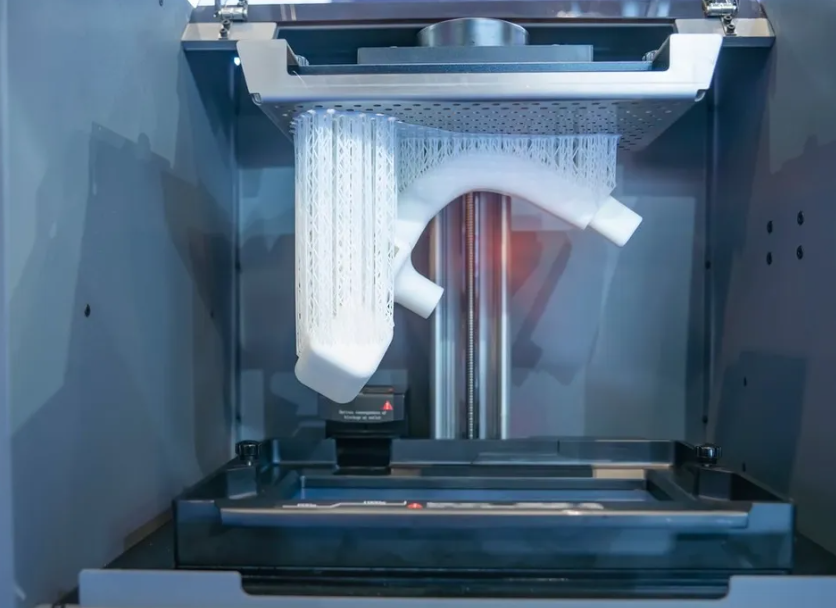
تفجوشی لیزری انتخابی (Selective Laser Sintering) یا SLS
یک روش چاپ سهبعدی است که از پودرهای پلیمری برای ساخت قطعات، اجزا و نمونههای اولیه استفاده میکند. در این فرآیند، از یک لیزر برای تف جوشی (زینترینگ) پودرهای پلیمری استفاده میشود تا یک شیء سهبعدی جامد ایجاد گردد.
نحوه عملکرد SLS:
آمادهسازی مواد: ابتدا مواد پودر پلیمری آماده میشوند. این مواد ترموپلاستیک هستند و در محفظه ساخت دستگاه پرینتر SLS قرار میگیرند.
ایجاد مدل سه بعدی: مدل سه بعدی با استفاده از نرمافزار CAD طراحی شده و به فرمت سازگار با تجهیزات چاپ SLS تبدیل میشود.
تف جوشی لیزری: پودر روی سکوی ساخت پخش میشود و لیزر با حرکت در سطح مقطع مدل، ذرات پودر را ذوب کرده و به هم متصل میکند. پودر سینتر نشده در طول ساخت از شی پشتیبانی میکند و نیاز به استفاده از ساختارهای پشتیبانی نیست.
تکرار لایهها: پس از اتمام یک لایه، سکو کمی به سمت پایین حرکت میکند و لایه جدیدی از پودر روی آن پخش میشود. این چرخه تا زمان تکمیل کل شیء تکرار میشود.
خنکسازی و پودرزدایی: پس از اتمام فرآیند چاپ، قطعات در پودر مدفون هستند و نیاز است تا مخزن پودر به آرامی خنک شود. سپس قطعات با فشار هوا یا سایر ابزارها پودرزدایی میشوند.
مزایای SLS:
تولید قطعات کاربردی: SLS امکان ایجاد قطعات کاربردی و نهایی با خواص مکانیکی و هندسههای دقیق را فراهم میکند.
هزینه تولید مقرون به صرفه: تهیه مواد اولیه نسبتاً ارزان است و میتوان از این روش برای تولید سفارشی و تیراژ پایین با هزینه کمتر استفاده کرد.
فرآیند تولید سریع: SLS امکان تولید نمونههای اولیه و قطعات نهایی را در یک روز فراهم میکند.
خواص مکانیکی خوب: قطعات SLS دارای خواص مکانیکی ایزوتروپیک خوبی هستند و برای ساخت قطعات کاربردی و نمونهسازیهای صنعتی مناسباند.
عدم نیاز به ساپورت: عدم نیاز به سازه ساپورت، آزادی بالایی در طراحی و ساخت قطعات با هندسههای پیچیده فراهم میکند.
معایب SLS:
فراهم نبودن امکان تولید قطعات بزرگ.
کاربردهای SLS:
تولید قطعات مورد استفاده در صنایع هوافضا، خودروسازی و مراقبتهای بهداشتی.
تولید نمونههای اولیه، قطعات یدکی و حتی تولید انبوه در داخل شرکتها.
به طور کلی، SLS یک فناوری قدرتمند برای تولید قطعات پلاستیکی با کیفیت بالا و خواص مکانیکی مناسب است و به عنوان یک جایگزین برای روشهای سنتی مانند قالبگیری تزریقی مورد توجه قرار میگیرد. پیشرفتهای تکنولوژیک باعث شده تا پرینترهای سه بعدی SLS مقرون به صرفهتر و جمعوجورتر شوند و امکان استفاده از آنها در دفاتر کار و محیطهای صنعتی فراهم گردد.
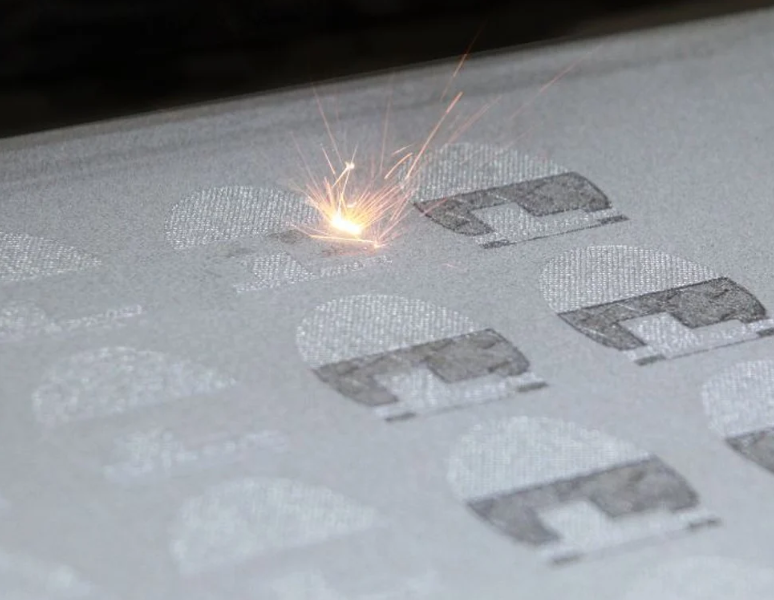
ذوب لیزری انتخابی (Selective Laser Melting یا SLM)
یک فناوری پیشرفته در چاپ سهبعدی است که به طور خاص برای تولید قطعات فلزی با کیفیت بالا و دقت بسیار بالا طراحی شده است. این روش به عنوان یکی از روشهای ساخت افزایشی (Additive Manufacturing) شناخته میشود و به دلیل تواناییاش در ایجاد اشکال پیچیده و هندسههای متنوع، در صنایع مختلف مورد استفاده قرار میگیرد.
نحوه عملکرد SLM
آمادهسازی مواد:
در این فرآیند، پودر فلزی (مانند تیتانیوم، فولاد ضد زنگ یا آلومینیوم) به صورت یکنواخت بر روی سطح پلتفرم ساخت پخش میشود.
ذوب لیزری:
یک لیزر پرقدرت به صورت انتخابی بر روی پودر تابیده میشود و آن را ذوب میکند. این عمل باعث میشود که ذرات پودر به هم متصل شده و یک لایه جامد تشکیل دهند.
تکرار لایهها:
پس از اتمام یک لایه، پلتفرم ساخت به سمت پایین حرکت کرده و لایه جدیدی از پودر بر روی آن پخش میشود. این فرآیند تا تکمیل کل مدل ادامه مییابد.
محیط کنترلشده:
کل فرآیند در یک محیط کنترلشده انجام میشود، معمولاً در گاز بیاثر (مانند آرگون) برای جلوگیری از اکسیداسیون مواد.
مزایا و معایب SLM
مزایا
توانایی تولید اشکال پیچیده:
SLM قادر است هندسههای پیچیدهای را تولید کند که دستیابی به آنها با روشهای تولید سنتی دشوار یا غیرممکن است.
کاهش ضایعات مواد:
این روش تنها مقدار لازم از مواد را مصرف میکند و ضایعات را به حداقل میرساند.
سفارشیسازی سریع:
امکان تولید سریع نمونههای اولیه و قطعات سفارشی را فراهم میآورد.
خواص مکانیکی مطلوب:
قطعات تولید شده با SLM دارای خواص متالورژیکی مشابه یا بهتر از قطعات تولید شده با روشهای سنتی هستند.
معایب
هزینه بالا:
تجهیزات و فرآیند SLM ممکن است هزینه بالایی داشته باشد، به ویژه برای قطعاتی که بهینه نشدهاند.
نیاز به مهارت تخصصی:
طراحی و ساخت قطعات با استفاده از SLM نیازمند دانش و مهارت تخصصی است.
محدودیت اندازه:
معمولاً محدود به تولید قطعات نسبتاً کوچک است.
کاربردها
SLM عمدتاً در صنایع زیر کاربرد دارد:
پزشکی: تولید ایمپلنتها و اجزای دستگاههای پزشکی.
خودروسازی: نمونهسازی سریع و تولید قطعات سفارشی.
هوافضا: ساخت اجزای پیچیده مانند مجاری و سایر قطعات حساس.
ابزارسازی: تولید کانالهای خنککننده و سایر ابزارهای دقیق.
SLM با توجه به مزایای خود، به عنوان یک فناوری نوآورانه در صنعت چاپ سهبعدی فلزی شناخته میشود و انتظار میرود که با پیشرفت تکنولوژی، کاربردهای بیشتری پیدا کند.
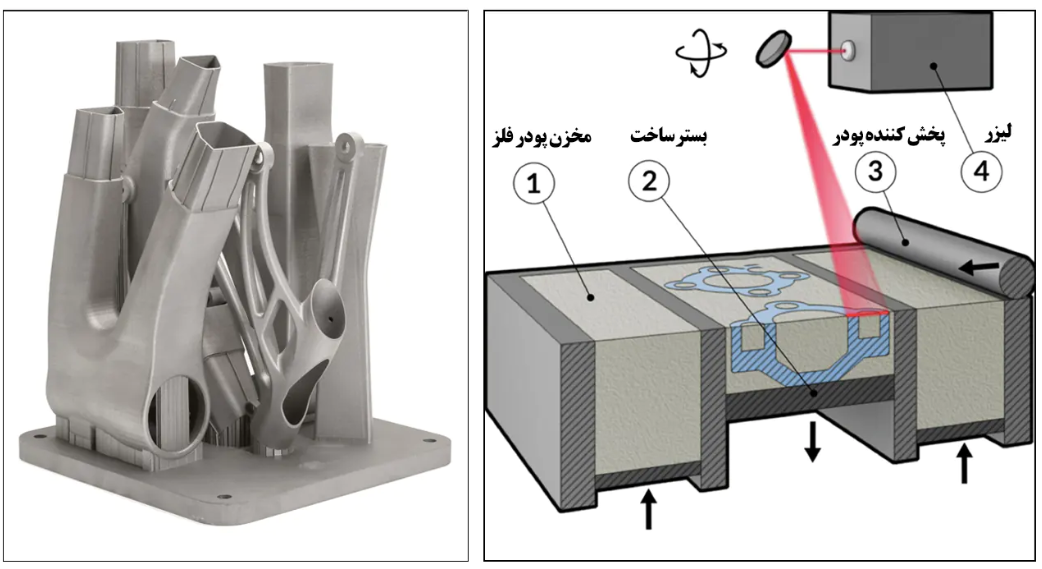
ساخت اشیاء چند لایه (Laminated Object Manufacturing یا LOM)
یک روش چاپ سهبعدی است که به وسیله آن میتوان اشیاء فیزیکی را از لایههای ورقهای کاغذ یا پلاستیک تولید کرد. این تکنیک ابتدا توسط شرکت کالیفرنیایی Helisys Inc توسعه یافته و به عنوان یک روش سریع و مقرون به صرفه برای نمونهسازی سهبعدی شناخته میشود.
نحوه عملکرد LOM
تغذیه ورقها:
ورقهای کاغذ یا پلاستیک از یک رول تغذیه شده و به وسیله یک غلتک حرارتی به لایه قبلی چسبانده میشوند.
برش لایهها:
پس از چسباندن هر لایه، یک لیزر یا تیغ متصل به کامپیوتر، لایهها را به اشکال دلخواه برش میزند. این برشها به شکل کانتورهای محیطی هر مقطع از قطعه انجام میشود.
تکرار فرآیند:
این فرآیند تا زمانی که شیء مورد نظر به حجم ایدهآل برسد، ادامه پیدا میکند. در نهایت، قطعه از روی هم قرار گرفتن لایههای متوالی مواد ورقهای ایجاد میشود.
پایان کار:
پس از اتمام چاپ، قطعه نهایی از دستگاه خارج شده و ممکن است نیاز به عملیات پسپردازش داشته باشد.
مزایا و معایب LOM
مزایا
سرعت بالا:
LOM یکی از سریعترین روشها برای تولید نمونههای اولیه است.
هزینه پایین:
استفاده از ورقهای کاغذی یا پلاستیکی باعث کاهش هزینه مواد اولیه میشود.
سازگاری با طراحیهای پیچیده:
این روش امکان تولید اشکال پیچیده را فراهم میکند.
معایب
کیفیت سطح پایینتر:
معمولاً کیفیت سطح قطعات تولید شده با LOM نسبت به روشهایی مانند SLA یا SLS پایینتر است.
محدودیت در مواد:
انتخاب مواد برای چاپ محدود به ورقهای کاغذی و پلاستیکی است که ممکن است خواص مکانیکی کمتری داشته باشند.
کاربردها
LOM بیشتر در کاربردهای زیر استفاده میشود:
تولید نمونههای اولیه برای طراحی و تست.
ساخت مدلهای مفهومی.
کاربردهای آموزشی و تحقیقاتی.
به طور کلی، LOM یک فناوری مفید برای تولید سریع و مقرون به صرفه نمونههای اولیه است، اگرچه ممکن است در مقایسه با دیگر روشهای چاپ سهبعدی در کیفیت نهایی محدودیتهایی داشته باشد.
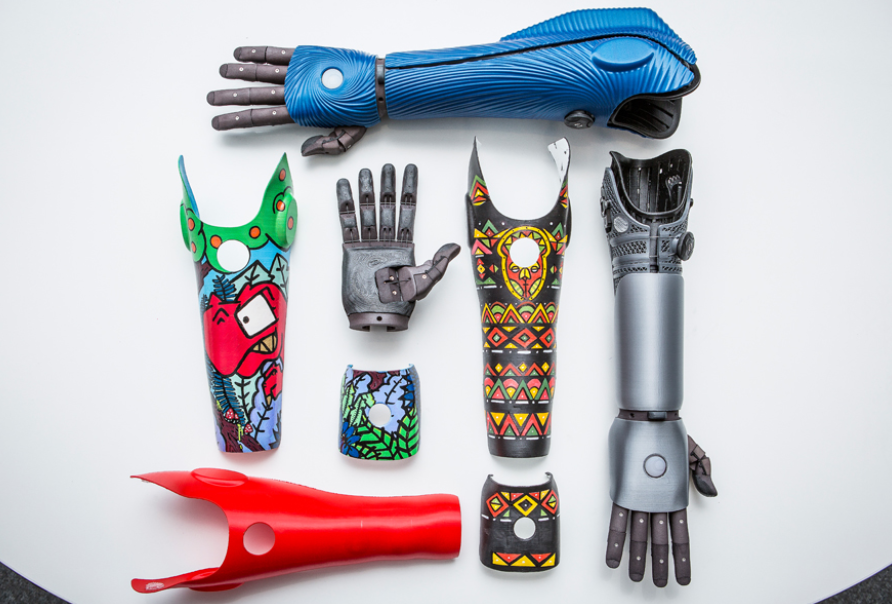
ذوب پرتو الکترونی (Electron Beam Melting یا EBM)
یک فناوری پیشرفته در چاپ سهبعدی است که از پرتوهای الکترونی برای ذوب و همجوشی پودرهای فلزی استفاده میکند. این روش به ویژه برای تولید قطعات فلزی با کیفیت بالا و دقت بسیار مناسب است و در صنایع مختلف کاربرد دارد.
نحوه عملکرد EBM
محفظه خلاء:
فرآیند EBM در یک محفظه خلاء انجام میشود تا از اکسیداسیون مواد جلوگیری شود. این شرایط محیطی به ویژه برای مواد فلزی بسیار واکنشپذیر اهمیت دارد.
تولید پرتو الکترونی:
یک تفنگ الکترونی الکترونها را از یک رشته تنگستن استخراج کرده و آنها را به سمت بستر پودر فلزی هدایت میکند.
ذوب پودر:
پرتو الکترونی با انرژی بالا به صورت انتخابی بر روی لایههای پودر تابیده میشود و آنها را ذوب میکند. این عمل باعث ایجاد لایههای جامد جدید میشود که به تدریج شکل نهایی قطعه را تشکیل میدهند.
تکرار لایهها:
پس از ذوب هر لایه، پلتفرم ساخت به سمت پایین حرکت میکند و لایه جدیدی از پودر بر روی آن قرار میگیرد. این فرآیند تا تکمیل کل مدل ادامه مییابد.
مزایا و معایب EBM
مزایا
کیفیت بالای قطعات:
قطعات تولید شده با EBM دارای خواص مکانیکی عالی و تراکم بالایی هستند (بیش از 99%).
امکان تولید اشکال پیچیده:
این فناوری امکان تولید هندسههای پیچیدهای را فراهم میآورد که با روشهای سنتی دشوار است.
کاهش تنش حرارتی:
EBM معمولاً تنش حرارتی کمتری نسبت به روشهای دیگر مانند SLM (ذوب لیزری انتخابی) ایجاد میکند.
معایب
هزینه بالا:
تجهیزات و فرآیند EBM معمولاً هزینهبر هستند و نیاز به سرمایهگذاری اولیه بالایی دارند.
محدودیت در مواد:
این فناوری بیشتر برای برخی فلزات خاص مانند تیتانیوم و آلیاژهای فولادی مناسب است.
کاربردها
EBM به طور گسترده در صنایع زیر کاربرد دارد:
پزشکی: تولید ایمپلنتها و پروتزها.
هوافضا: ساخت قطعات حساس مانند تیغههای توربین.
خودروسازی: تولید قطعات سفارشی و نمونههای اولیه.
EBM با توجه به مزایای خود، به عنوان یک فناوری نوآورانه در صنعت چاپ سهبعدی فلزی شناخته میشود و انتظار میرود که با پیشرفت تکنولوژی، کاربردهای بیشتری پیدا کند.
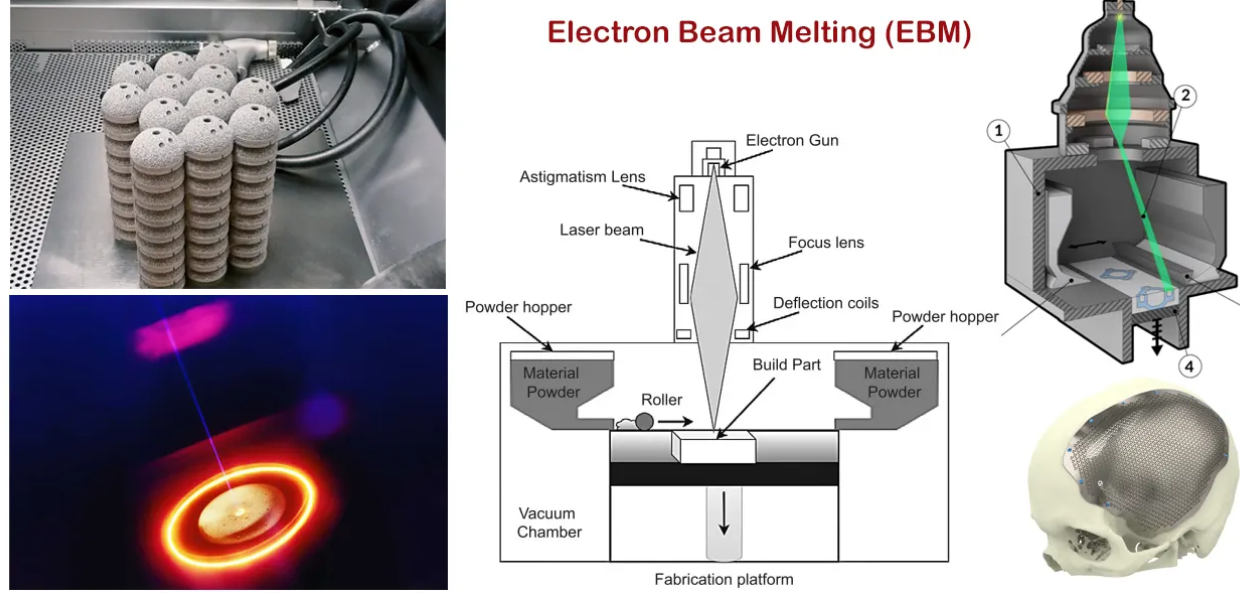
پرتاب چندگانه مواد فتوپلیمری (PolyJet)
یک فناوری پیشرفته در چاپ سهبعدی است که از روشهای متریال جتینگ برای تولید قطعات با کیفیت بالا استفاده میکند. این تکنیک به دلیل توانایی در تولید اشکال پیچیده و جزئیات دقیق، در صنایع مختلف بسیار محبوب است.
نحوه عملکرد PolyJet
تغذیه مواد:
در این روش، رزینهای فوتوپلیمر مایع به صورت کارتریجهای جداگانه در پرینتر قرار میگیرند.
پاشش قطرات:
هد پرینتر مشابه چاپگرهای جوهرافشان عمل میکند و صدها قطره کوچک از رزین را به طور همزمان بر روی بستر چاپ پخش میکند.
پخت با نور UV:
پس از پاشش هر لایه، یک منبع نور UV به قطرات تابیده میشود تا آنها را به سرعت سخت کند. این فرآیند باعث ایجاد لایههای جامد میشود.
تکرار لایهها:
پس از اتمام هر لایه، بستر چاپ به اندازه ضخامت یک لایه پایین میآید و فرآیند تکرار میشود تا زمانی که شیء سهبعدی کامل شود.
مزایا و معایب PolyJet
مزایا
دقت بالا:
PolyJet قادر است جزئیات بسیار دقیق و سطوح صاف را تولید کند.
تنوع مواد:
امکان استفاده از چندین نوع رزین با خواص مختلف (سخت، نرم، شفاف) در یک چاپ واحد وجود دارد.
تولید سریع:
این فناوری امکان تولید سریع نمونههای اولیه و قطعات نهایی را فراهم میآورد.
معایب
محدودیت در مواد:
انتخاب مواد محدود به رزینهای فوتوپلیمر است که ممکن است خواص مکانیکی کمتری نسبت به فلزات داشته باشند.
هزینه بالای تجهیزات:
پرینترهای PolyJet معمولاً هزینه بالایی دارند و نیاز به نگهداری دقیق دارند.
کاربردها
PolyJet به طور گسترده در صنایع زیر کاربرد دارد:
مدلسازی و نمونهسازی سریع: برای تولید مدلهای مفهومی و نمونههای اولیه.
صنعت پزشکی: تولید ایمپلنتها و ابزارهای پزشکی.
طراحی صنعتی: ساخت قطعات پیچیده با رنگها و بافتهای مختلف.
با توجه به مزایای خود، فناوری PolyJet یکی از گزینههای قدرتمند برای تولید قطعات با کیفیت بالا در دنیای چاپ سهبعدی محسوب میشود.
پرینت سهبعدی مولتیجت فیوژن (MJF)
یک فناوری نوآورانه تولید افزوده است که توسط شرکت HP توسعه یافته و به دلیل سرعت بالا و کیفیت بالای تولید قطعات، در صنایع مختلف مورد استفاده قرار میگیرد.
نحوه عملکرد MJF
پخش پودر:
در ابتدا، یک لایه نازک از پودر پلیمر بر روی بستر چاپ پخش میشود.
پاشش مواد:
سپس، هد پرینتر با استفاده از جتهای متعدد، یک عامل همجوشی (fusing agent) و یک عامل جزئیات (detailing agent) را به صورت انتخابی بر روی پودر میپاشد. عامل همجوشی باعث ذوب شدن پودر در نواحی مشخص شده میشود، در حالی که عامل جزئیات به حفظ کیفیت سطح کمک میکند.
حرارتدهی:
پس از پاشش، منبع گرمایی مادون قرمز بر روی لایهها عبور میکند و نواحی پوشش داده شده با عامل همجوشی را گرم میکند تا ذوب شوند و به یکدیگر متصل گردند.
تکرار لایهها:
بستر چاپ به اندازه ضخامت یک لایه پایین میآید و این فرآیند تا تکمیل کل مدل ادامه مییابد.
مزایا و معایب MJF
مزایا
سرعت بالا:
MJF قادر است قطعات را با سرعت بالا تولید کند، زیرا فرآیند همجوشی همزمان برای تمام نواحی پوشش داده شده انجام میشود.
کیفیت سطح عالی:
استفاده از عامل جزئیات باعث بهبود کیفیت سطح قطعات میشود.
نیاز به ساختار پشتیبان ندارد:
این فناوری امکان تولید اشکال پیچیده بدون نیاز به ساختارهای پشتیبانی را فراهم میآورد.
استحکام ایزوتروپیک:
قطعات تولید شده دارای استحکام یکنواخت در تمامی جهات هستند.
معایب
هزینه تجهیزات:
پرینترهای MJF معمولاً هزینه بالایی دارند و ممکن است برای برخی از کسبوکارها مقرون به صرفه نباشند.
محدودیت مواد اولیه:
این فناوری عمدتاً محدود به مواد پلیمری است، که ممکن است برای برخی کاربردها کافی نباشد.
کاربردها
MJF در صنایع مختلف کاربرد دارد:
خودروسازی: تولید قطعات یدکی و نمونههای اولیه.
هوافضا: ساخت اجزای پیچیده و سبک.
پزشکی: تولید ابزارهای پزشکی و ایمپلنتها.
محصولات مصرفی: تولید اسباب بازیها و اکسسوریها.
با توجه به مزایای خود، فناوری MJF یکی از گزینههای قدرتمند برای تولید قطعات با کیفیت بالا در دنیای چاپ سهبعدی محسوب میشود.
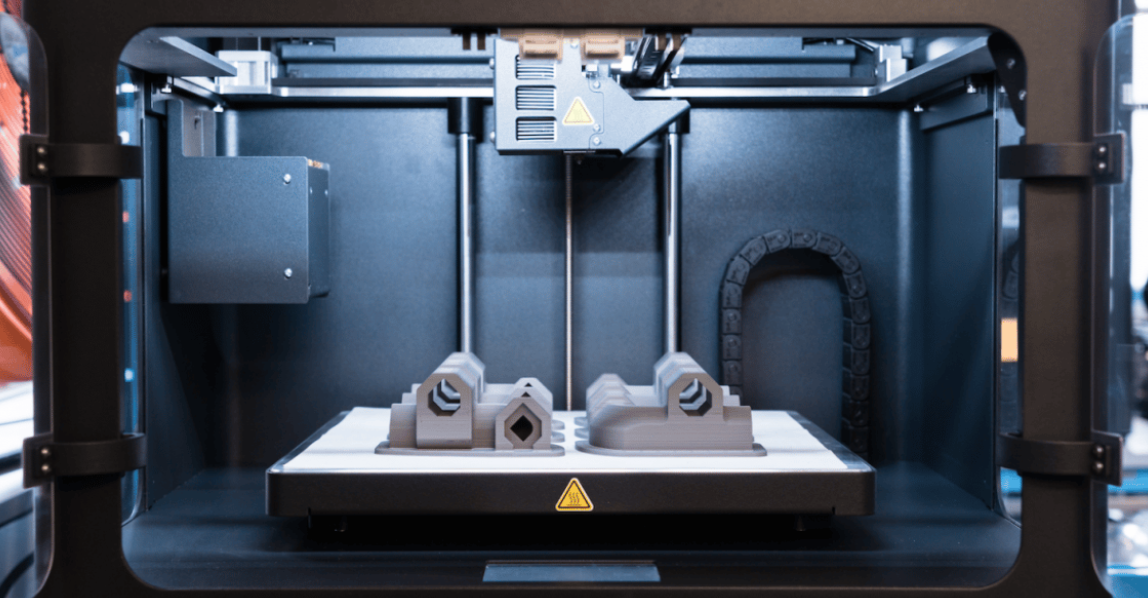
سالها تحقیق روی مواد و روشهای پرینت سهبعدی منجر به توسعه دهها شیوه جدید شده است. بهطور کلی، چهار روش عمده در این زمینه وجود دارد:
اکستروژن گرم مواد:
این روش شامل استفاده از ترموپلاستیکها به عنوان مواد اولیه است که معمولاً در پرینترهای FDM (مدلسازی رسوب ذوبشده) و FFF (مدلسازی فیلامنت ذوبشده) به کار میروند. در این فرآیند، مواد به صورت رشتههای نازک (فیلامنت) به نازل اکسترودر منتقل میشوند و با حرارت بالا ذوب شده و بر روی بستر چاپ رسوب میکنند.
اکستروژن سرد مواد:
این روش مشابه اکستروژن گرم است، اما در آن از مواد با دمای پایینتر استفاده میشود. این نوع اکستروژن معمولاً برای مواد حساس به حرارت یا ترکیبات خاصی که نیاز به دماهای پایین دارند، کاربرد دارد.
شیوههای پرداخت بر بستر پودر:
این دسته شامل تکنیکهایی مانند SLS (تفجوشی لیزری انتخابی)، EBM (ذوب پرتو الکترونی) و SLM (ذوب لیزری انتخابی) است. در این روشها، پودرهای فلزی یا پلیمری با استفاده از انرژی متمرکز (مانند لیزر یا پرتو الکترونی) ذوب شده و به هم متصل میشوند تا قطعات جامدی ایجاد کنند.
مخزن رزین:
این روش شامل فناوریهایی مانند SLA (استریولیتوگرافی) و DLP (پردازش دیجیتال نور) است که در آنها از رزینهای فوتوپلیمر استفاده میشود. در این فرآیند، نور UV یا دیگر منابع نوری برای سخت کردن رزین مایع به کار میرود و قطعات سهبعدی تولید میشوند.
این چهار روش عمده، پایهگذار بسیاری از فناوریهای نوین در صنعت چاپ سهبعدی هستند و هر کدام مزایا و معایب خاص خود را دارند که بر انتخاب مناسبترین روش تأثیرگذار است.